What Technicians Need To Consider When Shopping For The Best Drill Bits Tooling
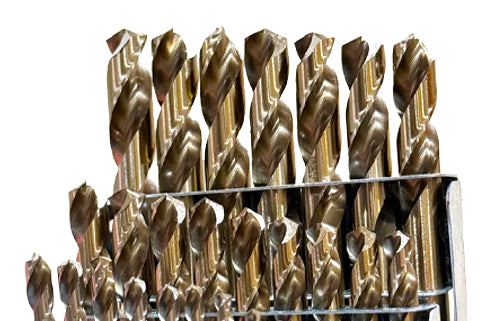
It all depends on the application!
There are many different types of metal combinations used for manufacturing drill bits. Steel is the most common material used for drill bit production. In its basic form, it is best used for drilling softer materials such as wood or non-ferrous materials like aluminum, brass, lead, etc. However, when it comes to drilling material with a higher carbon content or chromium oxide (stainless steel), ferrous metals (ex. high-speed steel, black oxide, cobalt steel, and titanium nitride) require the drill bit to cut quickly and accurately. Therefore, the task of selecting the correct drill bit is just as important as selecting the correct speed. This is not a “one size fits all” application.
High-speed steel is the least expensive and most basic drill bit which is fine for most metal-drilling tasks. However, to drill through abrasive metals such as cast iron, stainless steel, or hardened steel, the drill bit has to be harder and more capable to retain its cutting capability. Cobalt or black oxide for example are better for these applications. Although these bits are more expensive, they are capable of boring more holes and sustaining this capability longer before becoming dull. Moreover, some bits have a special coating that is applied in the manufacturing process in order to reduce friction and dissipate heat. Titanium nitride (TiN) is a good example, which can last up to six times longer than high-speed steel bits.
Accuracy in cut quality and capability. Although they both look the same, tooling bits are superior in quality of materials, grind angle (lip), diameter tolerance and how straight the bit is formed. Tooling bits are also referred to as machine grade or machine-shop grade, due to their predictability in a controlled cut or machining operation. Regular drill bits are used where accuracy and cut control are unimportant.
Factors to consider are
The type of drill bit will depend on the quality of the metal. To drill through stainless steel, use black oxide or cobalt steel bits because they are capable of drilling harder materials and more holes before becoming dull. High-speed steel drill bits will work fine on most other non-hardened metals. Once again, keep in mind the application. For example, drilling an exhaust manifold bolt is not that challenging. Drilling one that has been through thousands of heat and cooling duty cycles changes the properties of the steel or stainless. Furthermore, it increases the hardness of the material, making it a challenge to drill it in.
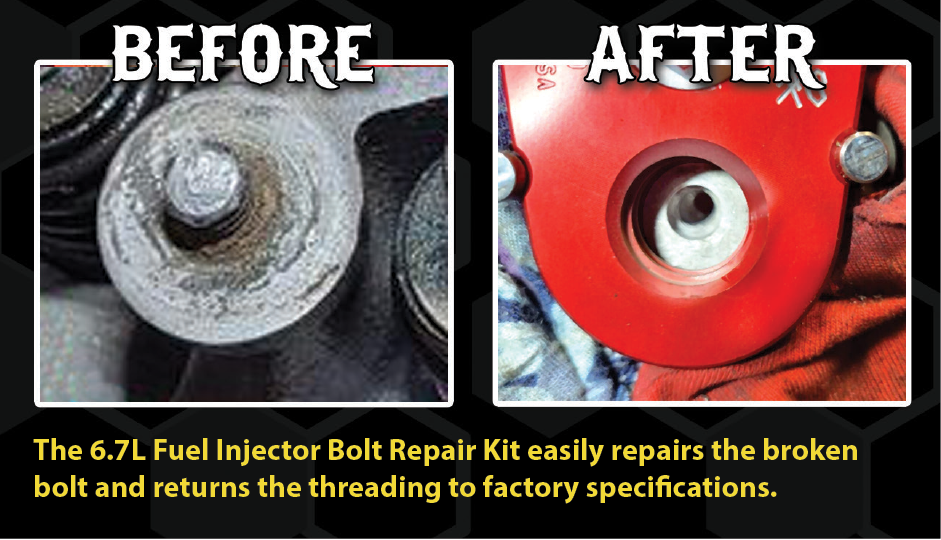
A cutting edge is the tip of the cutter tooth of a drill bit. The point angle is formed by the cutting edge and the tool axis (centerline of the bit). It is determined by the correct amount of lip (angle between tip and cutting edge) clearance. The greater the lip angle the more aggressive the bit will cut. A smaller angle (flattening the bit) has more web surface area which cuts slower because of the size of the web surface. However, this can be more difficult to drill harder materials.
ProMAXX® machine-grade tooling bits are ground at 135° cutting angle (lip) with a split point. Flat ground bits cut slower and are long-lasting but less accurate and will walk while drilling. Split point ground bits will stay on center to reduce walking because they have four cutting edges and distribute loads better. They work well on curved shapes and alloy and stainless steel because it creates smaller chips to minimize clogging holes and breaking bits. It also has a thinner web, requiring less force, because there is less heat and less chance of work hardening.
Naturally, spinning a drill bit too fast or with too much force will cause it to overheat, get dull faster, and break. Some metals like steel and larger drills require even slower speeds. See ProMAXX® drill and speeds attached.
PRODRILL PLATINUM DRILL BITS
The type of metal that is being machined will best determine the correct drill bit that needs to be used. Alignment is also the main culprit for broken bits. Applying pressure in line with the bit is best but not always possible, due to obstructions where the bit is to be used. Nevertheless, bending a bit even as little as four degrees will cause a high-quality bit to fracture. Be sure to use the best type of drill bit for the material to be cut. At ProMAXX®, we have taken the guesswork out of the task. High-quality bits, such as ours, can be used in multiple applications whereas lower-quality bits cannot. For a more detailed explanation, check out on "Why Do Drill Bits Break?".
To prevent a drill bit from wandering, many technicians choose to utilize a center punch to create a dimple in order to keep the drill in place. However, this is not foolproof. For accuracy in commercial machine shops, jigs or fixtures are commonly used. Bringing machine shop accuracy to an expensive cylinder head during an under-the-hood operation is critical. ProMAXX® engineered performance products are designed to do just that! These kits make it easier, more predictable, and far more productive. Even the most inexperienced technician can’t mess it up. ProMAXX® ProKits include all of the necessary components and machine-grade tooling to get the job done quickly and more productively. (See ProMAXX® Kit Comparison.)
Using a lubricant or cutting fluid such as ProMAXX® ProLube can reduce friction and heat buildup and make drilling. However, aluminum, brass, or cast iron, are easier-to-drill metals and may not need lubrication.
It is also a good idea to remove any sharp edges, or in shop terms, deburr the hole or damaged remnant in preparation for removal in an exhaust manifold repair. Check out our ProMAXX® ProCutter™. The aggressive cutting blade can cut a damaged stud flat, remove the burr, and remove the corrosion in just five seconds. It is an excellent addition for broken exhaust manifold stud extractions. Removing any burrs eliminates the risk of broken bolts getting hung up during extraction, which can result in a broken extractor.
Drill bits, like any tool, are designed specifically for different applications; each varying in size and composition. By knowing what you want your drill bit to do, you can make the right selection the first time, saving time and money and getting the job done much more productively. ProMAXX® has done research on thousands of broken bolt extraction repairs and has taken the guesswork out of the job. If you have questions on what tooling you need for your next repair, give the experts at ProMAXX® a call at (724) 941-0941.
Recommended Tooling Bits from ProMAXX Tool.
Superior quality machine-shop-grade tooling made from M42 cobalt. Micro-edge for walk-free machining and quick penetration. Short length for tight areas, thin web for fast clean drilling and chip clearing. Most bits stop cutting at Rc35, these will cut even harder metals up to and including Rc55 and titanium. Compatible with PPT125 ProTractor™ and 125 ProBushings. Meets and exceeds most tooling specifications including Aerospace. .125” Dia. +.000” - .002”.
NEW AT PROMAX
-
SAVE: 13%
Ford F-150 Rear Axle Repair Kit For 2021–2023 Trucks w/ Trailer Tow Max Duty Package & 9.75-inch Heavy-Duty Axle
Part#: PMXFRA500PROOriginal price $399.95Original price $399.95 - Original price $399.95Original price $399.95Current price $349.95$349.95 - $349.95Current price $349.95Original price $399.95Original price $399.95 - Original price $399.95Original price $399.95Current price $349.95$349.95 - $349.95Current price $349.95SAVE: 13% -
Forcing Screw Alternative to Ford 2020-2022 Explorer Recall Special Service Tool part# 204-594 "Thunderbolt"
Part#: PMX204-594Original price $0.00 - Original price $0.00Original price $0.00$149.95$149.95 - $149.95Current price $149.95Original price $0.00 - Original price $0.00Original price $0.00$149.95$149.95 - $149.95Current price $149.95 -
SAVE: 25%
Ford Power Stroke 6.7L Fuel Injector Copper Compression Seal Puller and Seal Saver ProKit
Part#: PMXISPS200BSEOriginal price $199.95Original price $29.95 - Original price $199.95Original price $199.95$29.95 - $149.95$29.95 - $149.95Current price $29.95Fuel Injector Seal Puller/Saver ProKit Part #: PMXISPS200PRO Introducing the cutting-edge Ford Power Stroke 6.7L Fuel Injector Copper Compression S...
VIEW MOREOriginal price $199.95Original price $29.95 - Original price $199.95Original price $199.95$29.95 - $149.95$29.95 - $149.95Current price $29.95SAVE: 25% -
Ford 6.7L Power Stroke Diesel EGR Tube Broken Bolt Repair Kit - Nino
Part#: PMXN200PROOriginal price $499.95 - Original price $749.95Original price$499.95 - $749.95$499.95 - $749.95Current price $499.95Nino EGR Tube ProKit Part #: PMXN200PRO 6.7L Ford Power Stroke Diesel Exhaust Gas Recirculation EGR Repair Kit - Nino The ProMAXX® EGR (Nino™) repa...
VIEW MOREOriginal price $499.95 - Original price $749.95Original price$499.95 - $749.95$499.95 - $749.95Current price $499.95 -
Ford 6.7L Diesel Power Stroke Fuel Injector Broken Bolt Repair Kit - Nico
Part#: PMXO200PROOriginal price $29.95 - Original price $699.95Original price $549.95$29.95 - $699.95$29.95 - $699.95Current price $29.95Now, Take $100 Off Nico ProKit PlusAnd…Get an Extra Insert - That’s a $179 Value! Ford 6.7L Power Stroke Diesel Hold-Down Bolt Repair ProKit Plus #...
VIEW MOREOriginal price $29.95 - Original price $699.95Original price $549.95$29.95 - $699.95$29.95 - $699.95Current price $29.95

SHIPPING INFO
For Saturday delivery or special shipping instructions, please contact ProMAXX Tool M-F 8 a.m. – 5 p.m. EST at 724-941-0941. Expedited Orders Placed by 1pm EST will be Processed Same Day | UPS Ground Processing Time is 1-3 Business Days

WARRANTY INFO
Offering a range of policies

NEED HELP
Contact our support team today
724-941-0941

Promaxx Tool Address
1121 Boyce Road
Suite #2000
Pittsburgh, PA 15241
Any motor company logo on this site is a Registered Trademark. ProMAXX Tool is not affiliated with any of the motor companies on this site.